The structure and design of a pure electric vehicle is different from that of a traditional internal combustion engine driven vehicle. It is also a complex system engineering. It needs to integrate power battery technology, motor drive technology, automotive technology and modern control theory to achieve an optimal control process. In the development plan of electric vehicle science and technology, the country continues to adhere to the R&D layout of "three vertical and three horizontal", and further highlights the research on common key technologies of "three horizontal" according to the technology transformation strategy of "pure electric drive", that is, the research on drive motor and its control system, power battery and its management system, and powertrain control system. Each major manufacturer formulates its own business development strategy according to the national development strategy.
The author sorts out the key technologies in the development process of a new energy powertrain, providing a theoretical basis and reference for the design, testing, and production of the powertrain. The plan is divided into three chapters to analyze the key technologies of electric drive in the powertrain of pure electric vehicles. Today, we will first introduce the principle and classification of electric drive technologies.
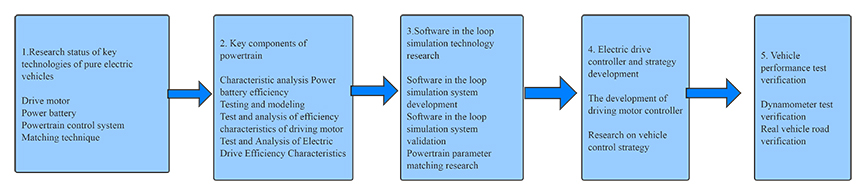
Figure 1 Key Links in Powertrain Development
At present, the core key technologies of pure electric vehicle powertrain include the following four categories:
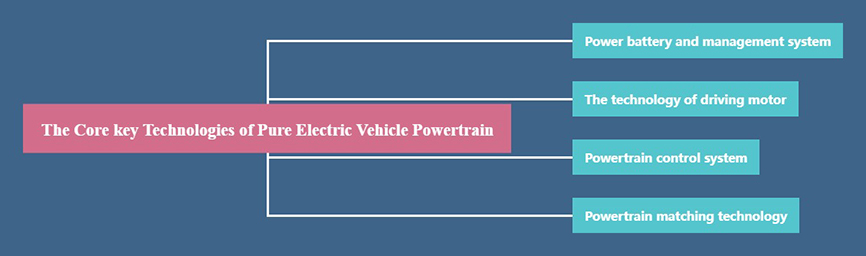
Figure 2 The Core Key Technologies of Powertrain
The Definition of Driving Motor System
According to the status of the vehicle power battery and requirements of vehicle power, it converts the electric energy output by on-board energy storage power generation device into mechanical energy, and the energy is transmitted to the driving wheels through the transmitting device, and parts of vehicle mechanical energy is converted into electric energy and fed back into the energy storage device when the vehicle brake. The electric driving system includes motor, transmission mechanism, motor controller and other components. The design of technical parameters of electric energy driving system mainly includes power, torque,speed,voltage,transmission ratio of reducing, power supply capacitance, output power, voltage, current, etc.
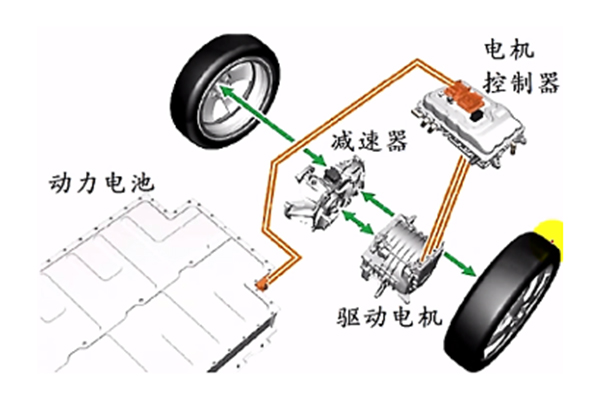
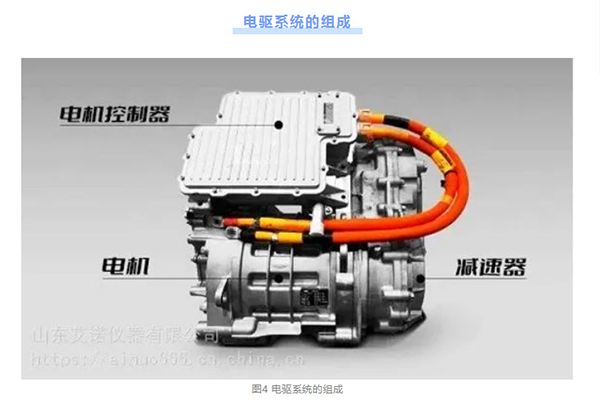
1) Motor controller
Also called inverter, it changes the direct current input by the power battery pack into alternating current. Core components:
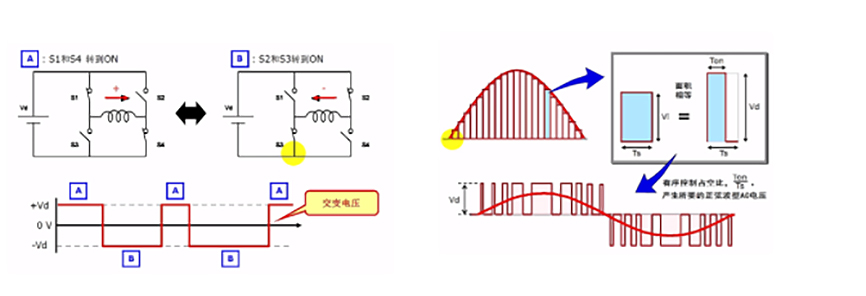
◎ IGBT: power electronic switch, principle: through the controller, control IGBT bridge arm to close a certain frequency and sequence switch to generate three-phase alternating current. By controlling the power electronic switch to close, the alternating voltage can be converted. Then the AC voltage is generated by controlling the duty cycle.
◎ Film capacitance: filtering function; current sensor: detecting the current of three-phase winding.
2) Control and driving circuit: computer control board, driving IGBT
The role of the motor controller is to convert DC to AC, receive each signal, and output the corresponding power and torque. Core components: power electronic switch, film capacitor, current sensor, control drive circuit to open different switches, form currents in different directions, and generate alternating voltage. Therefore, we can divide the sinusoidal alternating current into rectangles. The area of the rectangles is converted into a voltage with the same height. The x-axis realizes the length control by controlling the duty cycle, and finally realizes the equivalent conversion of the area. In this way, the DC power can be controlled to close the IGBT bridge arm at a certain frequency and sequence switch through the controller to generate three-phase AC power.
At present, the key components of the drive circuit rely on imports: capacitors, IGBT/MOSFET switch tubes, DSP, electronic chips and integrated circuits, which can be independently produced but have weak capacity: special circuits, sensors, connectors, which can be independently produced: power supplies, diodes, inductors, multilayer circuit boards, insulated wires, radiators.
3) Motor: convert three-phase alternating current into machinery
◎ Structure: front and rear end covers, shells, shafts and bearings
◎ Magnetic circuit: stator core, rotor core
◎ Circuit: stator winding, rotor conductor
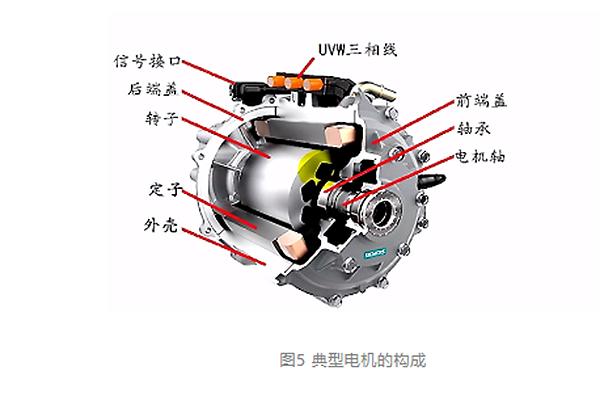
4) Transmitting Device
The gearbox or reducer transforms the torque speed output by the motor into the speed and torque required by the whole vehicle.
Type of driving motor
The driving motors are divided into the following four categories. At present, AC induction motors and permanent magnet synchronous motors are the most common types of new energy electric vehicles. So we focus on the technology of AC induction motor and permanent magnet synchronous motor.
DC Motor | AC Induction Motor | Permanent Magnet Synchronous Motor | Switched Reluctance Motor | |
Advantage | Lower Cost, Low requirements of Control System | Low cost, Wide power coverage, Developed control technology, High reliability | High Power Density, High efficiency, small size | Simple Structure, Low requirements of Control System |
Disadvantage | High maintenance requirements, Low speed, Low torque, short lifetime | Small efficient areaLow Power Density | High cost Poor environmental adaptability | Large torque fluctuationHigh working noise |
Application | Small or mini low-speed electric vehicle | Electric Business Vehicle and Passenger cars | Electric Business Vehicle and Passenger cars | Mixture-power Vehicle |
1)AC Induction Asynchronous Motor
The working principle of an AC inductive asynchronous motor is that the winding will pass through the stator slot and the rotor: it is stacked by thin steel sheets with high magnetic conductivity. The three-phase electricity will pass through the winding. According to Faraday's electromagnetic induction law, a rotating magnetic field will be generated, which is the reason why the rotor rotates. The three coils of the stator are connected at an interval of 120 degrees, and the current-carrying conductor generates magnetic fields around them. When the three-phase power supply is applied to this special arrangement, the magnetic fields will change in different directions with the change of alternating current at a specific time, generating a magnetic field with uniform rotating intensity. The rotating speed of the magnetic field is called synchronous speed. Suppose a closed conductor is placed inside, according to Faraday's law, because the magnetic field is variable, The loop will sense the electromotive force, which will generate current in the loop. This situation is just like the current carrying loop in the magnetic field, generating electromagnetic force on the loop, and Huan Jiang starts to rotate. Using something similar to a squirrel cage, a three-phase alternating current will produce a rotating magnetic field through the stator, and the current will be induced in the squirrel cage bar shorted by the end ring, so the rotor starts to rotate, which is why the motor is called an induction motor. With the help of electromagnetic induction rather than directly connected to the rotor to induce electricity, insulating iron core flakes are filled in the rotor, so that the small size iron ensures the minimum eddy current loss.
2) AC synchronous motor
The rotor of synchronous motor is different from that of asynchronous motor. The permanent magnet is installed on the rotor, which can be divided into surface mounted type and embedded type. The rotor is made of silicon steel sheet, and the permanent magnet is embedded. The stator is also connected with an alternating current with a phase difference of 120, which controls the size and phase of the sine wave alternating current, so that the magnetic field generated by the stator is opposite to that generated by the rotor, and the magnetic field is rotating. In this way, the stator is attracted by a magnet and rotates with the rotor. Cycle after cycle is generated by stator and rotor absorption.
Conclusion: The motor drive for electric vehicles has basically become the mainstream, but it is not single but diversified. Each motor drive system has its own comprehensive index. Each system is applied in the existing electric vehicle drive. Most of them are asynchronous motors and permanent magnet synchronous motors, while some try to switch reluctance motors. It is worth pointing out that motor drive integrates power electronics technology, microelectronics technology, digital technology, automatic control technology, material science and other disciplines to reflect the comprehensive application and development prospects of multiple disciplines. It is a strong competitor in electric vehicle motors. In order to occupy a place in the future electric vehicles, all kinds of motors need not only to optimize the motor structure, but also to constantly explore the intelligent and digital aspects of the control system.
Post time: Jan-30-2023